The adhesive interface is a vital part of any wearable medical device. If it fails, the device can shift or detach, compromising performance and user safety. The skin is a complex, living organ that varies greatly from person to person—and even from one part of the body to another. Because of this complexity, adhesives used in wearable medical devices must be carefully engineered to be biocompatible, minimizing the risk of irritation, allergic reactions, or long-term skin damage.
Choosing the Right Adhesive
Because skin is complex in nature, choosing the right adhesive material for your wearable medical device is a crucial decision. Most stick-to-skin adhesives fall into two buckets: acrylic or silicone.
Acrylic adhesives feature a strong initial tack and last for an extended amount of time. They also have great moisture resistance for highly active individuals with rigorous lifestyles. Acrylic adhesives for stick to skin applications into wearable devices tend to be more cost effective than silicone adhesives, but they also can be harsher on sensitive skin.
Silicone adhesives are a soft, flexible, and breathable adhesive that appeal to users aiming for comfortability and the ‘forget-it’s-there’ feel. Its high biocompatibility is also a great choice in adhesive for products aiming to treat young children or infants’ sensitive skin. It may be a less aggressive tack than acrylic adhesives, but their wear time is still intended to be for an extended amount of time.
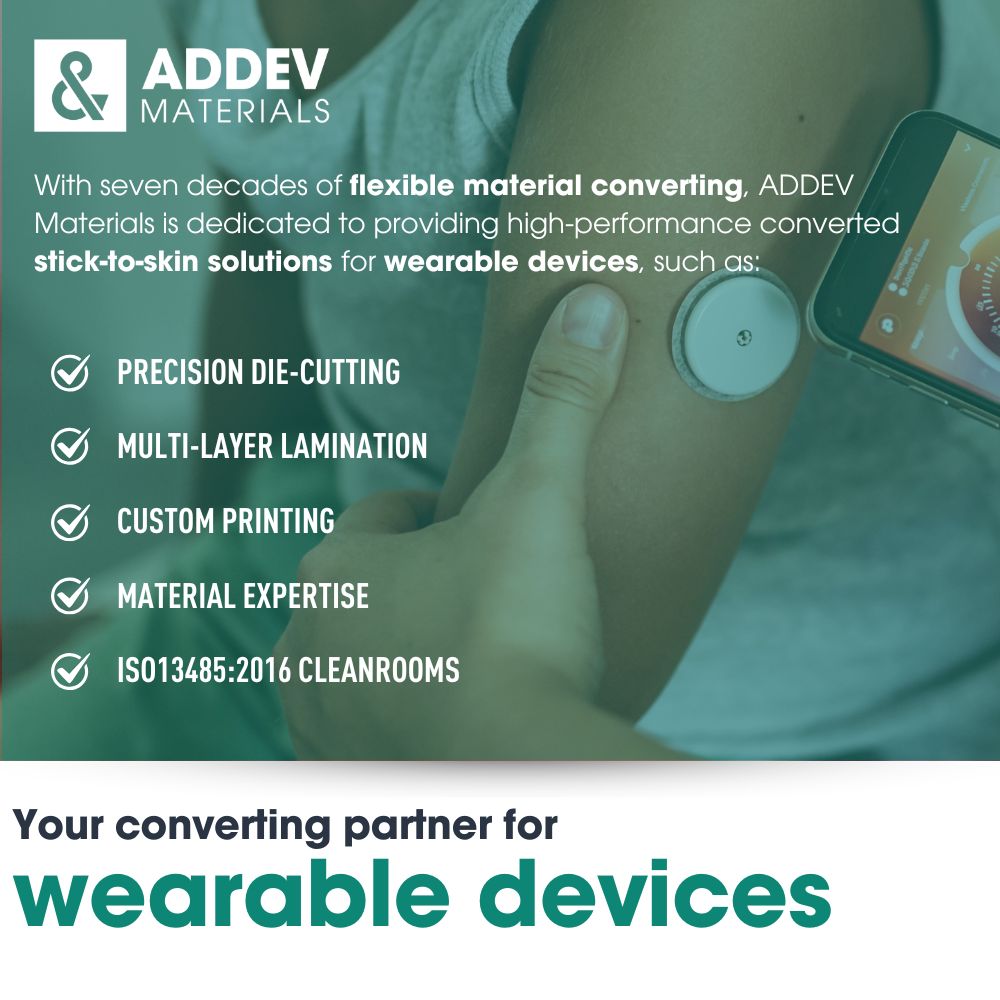
Converting Stick-to-Skin Adhesives into Wearable Devices
Once you’ve decided on a stick to skin adhesive that works best for your application, you’ll need to find a converting partner, like ADDEV Materials Healthcare, to convert the material into custom manufactured wearable devices.
With over seven decades of flexible material converting experience, ADDEV Materials Healthcare is dedicated to providing high-performance die cut materials solutions for the healthcare and MedTech industry. Our capabilities include:
- Precision die-cutting and laminating
- Custom slitting and multi-layer assemblies
- High-quality custom print
- Manufacturing in Class 7 and Class 8 cleanroom environments
- Full compliance with ISO 13485:2016 and FDA registered and ISO 13485:2016 certified
From prototyping to full-scale production, we help medical device manufacturers design and deliver wearable devices that patients can trust.
Looking for a material converting partner?
Visit https://addevhealthcare.com/capabilities/converting/ to learn more about our adhesive tape converting services and request a quote to get your diabetes medical device project started!